It Would Be So Much Easier If There Was Only One Problem to Deal With
The construction industry is a complicated business and is only getting more so in today’s fast-paced world. If you’re working in construction, or know someone who is, you know how overwhelming it can be trying to keep up with the business.
As complicated and overwhelming as the physical on-site construction portion is, the business part is equally daunting. This includes things like budgeting, scheduling, communication, labor issues, planning, and cash flow to mention a few.
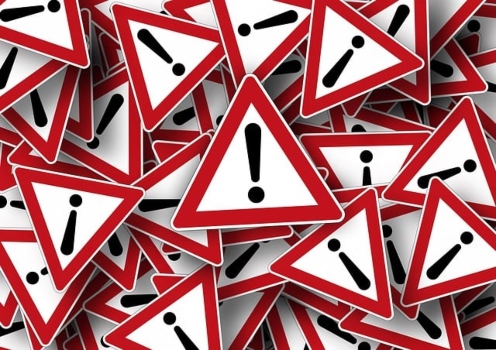
While researching the number one problem construction companies faced, it was confirmed that there is more than one problem, and they are common across the industry. Trying to ensure that projects stay on schedule, within budget, compliant with safety regulations, and running smoothly is difficult.
Wouldn’t it be great if there was only one problem?
Blackridge Research and Consulting is a market research and consulting organization. Their 2023 blog about the Major Challenges Facing the Construction Industry confirms what I’ve been saying for years.
Here are seven major construction industry problems –
- Cost overruns – This is one of the top construction industry problems. This is when a project exceeds its pre-planned budget. A McKinsey study estimates that 98% of large construction projects deal with cost overruns of more than 30%. This is often caused by poor cost estimates during the planning phase, design change requests, and payment delays. This results in lower profit margins, material shortages due to running out of funds, damage to the company’s reputation, and delays.
- Delays – The same McKinsey study also shows that 77% of construction projects are at least 40% late. Some factors that contribute to this can’t be controlled, i.e., weather, labor shortages, and equipment failures. But there are as many or more factors that can be controlled and prevented, including scheduling issues, project conflicts, and incorrect data. One of the best ways to reduce delays is through the use of technology but the industry’s willingness to adapt is a problem.
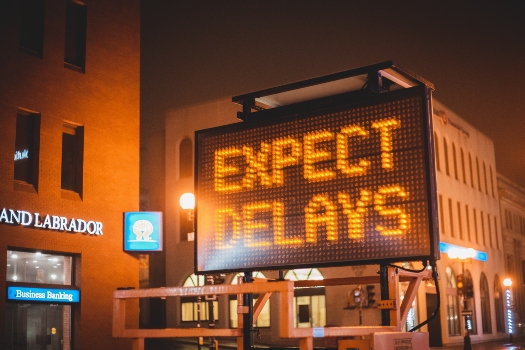
- Push back on new technology – This is one of the biggest problems in the construction industry. Its hesitancy to adopt new systems and processes that could make their companies more efficient is a problem. Even when construction companies acknowledge that there are solutions that they could benefit from they tend to stick to the mantra, “This is the way we’ve always done it”.
- Poor communication – One of the most prevalent construction issues is poor communication. Since construction projects require multiple people during the planning and construction, effective information exchange is crucial for the project’s success. Oftentimes, there’s a disconnect between the office and on-site workers. Poor communication is linked to a high percentage of construction problems resulting in complications such as unrealistic expectations and important tasks being overlooked. Keeping everyone in the loop by sharing obstacles and daily progress is a great way to avoid conflicts. Documented communication helps in cases where conflicts do arise.
- Poor planning and budgeting – When projects aren’t planned well it leads to unachievable goals that can result in construction issues like stagnant productivity. It helps to break larger goals down into smaller and more attainable ones with daily objectives. In terms of budgeting, incorrect estimates can disrupt progress and can cause projects to be delayed or dropped altogether. It can also lead to a reduction in company profit.
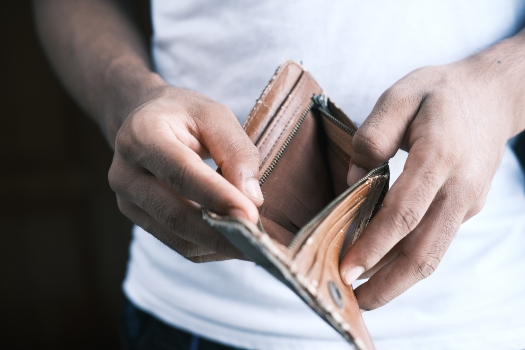
- Lack of organization and poor document management – This is another prevalent problem in the construction industry. Construction involves dealing with a lot of information, from contracts to material orders to receipts to insurance certificates. Document management is not something that people in construction typically like doing. Not doing it is inefficient and creates room for mistakes. Having a system that is digital allows for better access and centralizing important information.
- Cash flow issues – Problems with cash flow can cause construction challenges. Having a steady stream of funds is crucial to paying employees, subcontractors, vendors, and suppliers on time. When payments fall behind, it further disrupts cash flow, halting project progress and causing delays. The reason so many construction firms struggle with managing a project’s funding is that they rely on outdated systems. Having more modern solutions can ensure that all payments are made and accounted for.
Dealing with these problems is the reason I developed the business tools that I use at Timber Creek Construction every day. Seeing other construction companies struggling with the problems is the reason I started writing about them on Solution Building.
Now we’re going to make these tools available to construction companies that are tired of feeling trapped with no way out.
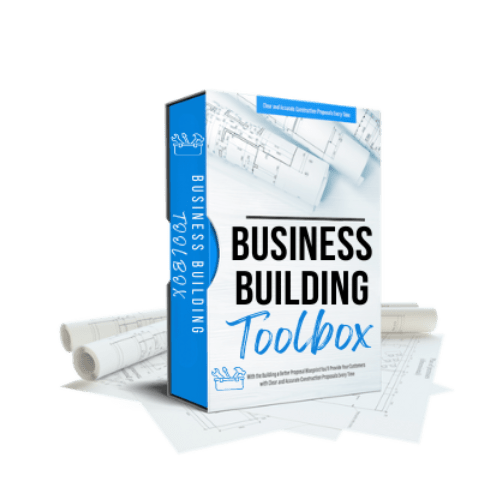
We plan to open our digital Business Building Toolbox next week. These tools and training are designed to help construction companies build the business that they always dreamed of. We will continue to add new tools and training in the future. If you would like more information about these tools and training and how they can help your construction company with these problems as well as others, schedule a free 30-minute consultation here.